Development of a Variable-Friction Shoe Surface Mechanism
Shared Reality Lab - McGill Centre for Intelligent Machines - Supervisor: Professor Jeremy Cooperstock
Interdisciplinary Design Project
“Completion of an individual project on an interdisciplinary theme with emphasis on a balanced combination of analysis and synthesis”
McGill University’s Shared Reality Lab studies methods of varying friction during natural walking for its applications in simulated environments and needed a mechanism to actively adjust friction. In seven months I created from scratch a device that replaces the heel of a boot and varies friction to simulate walking on surfaces from ice to concrete.
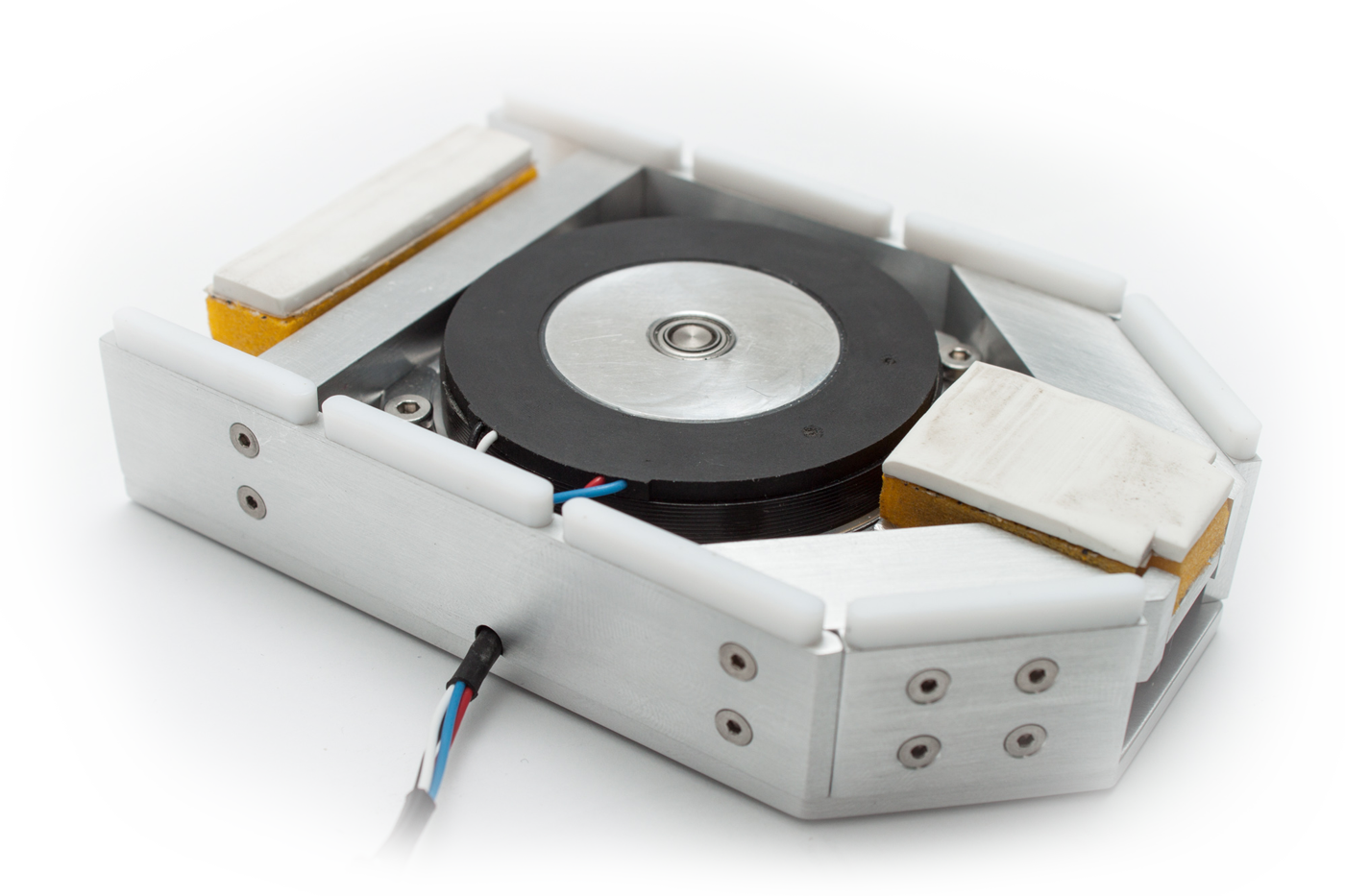
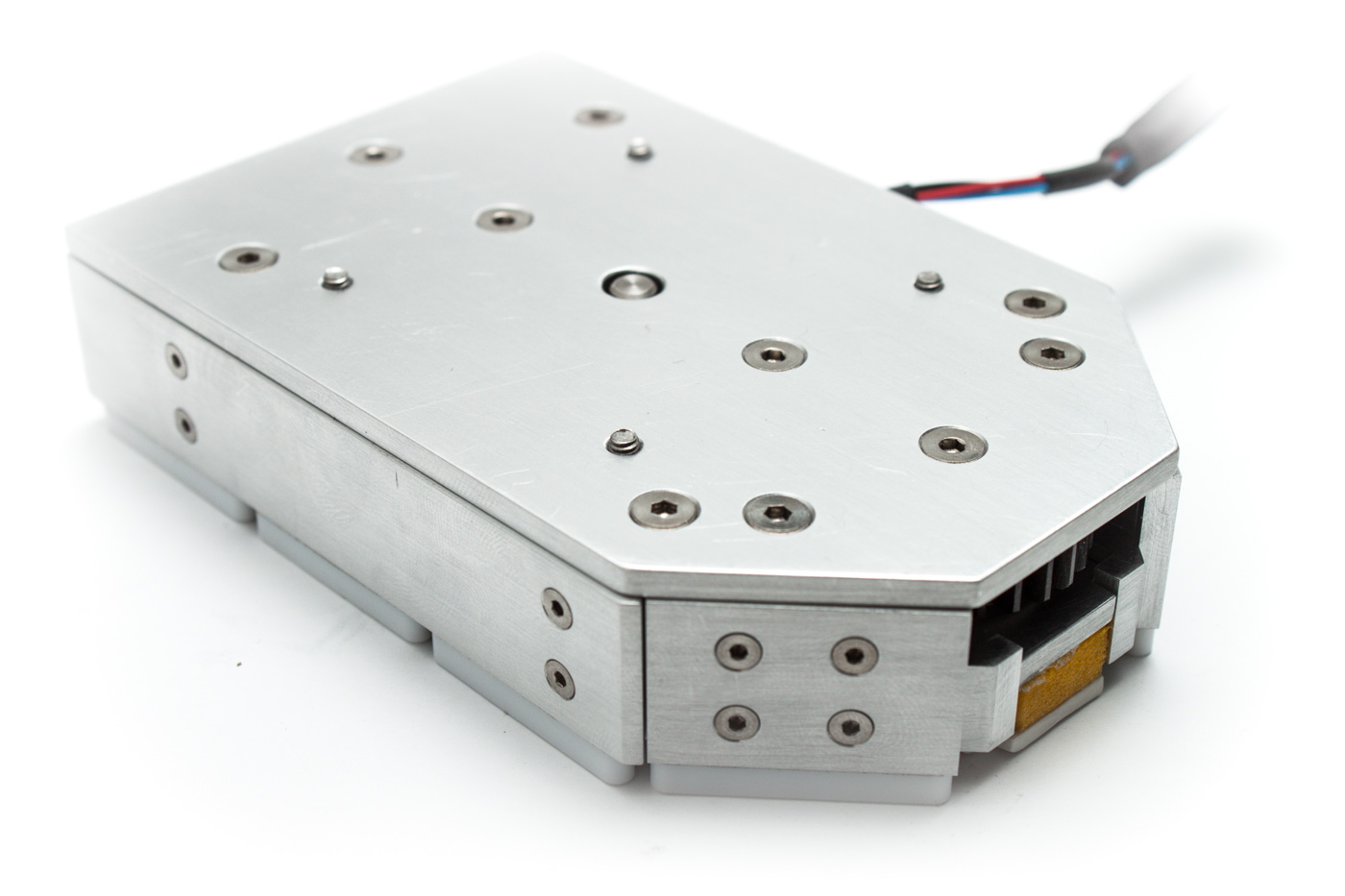
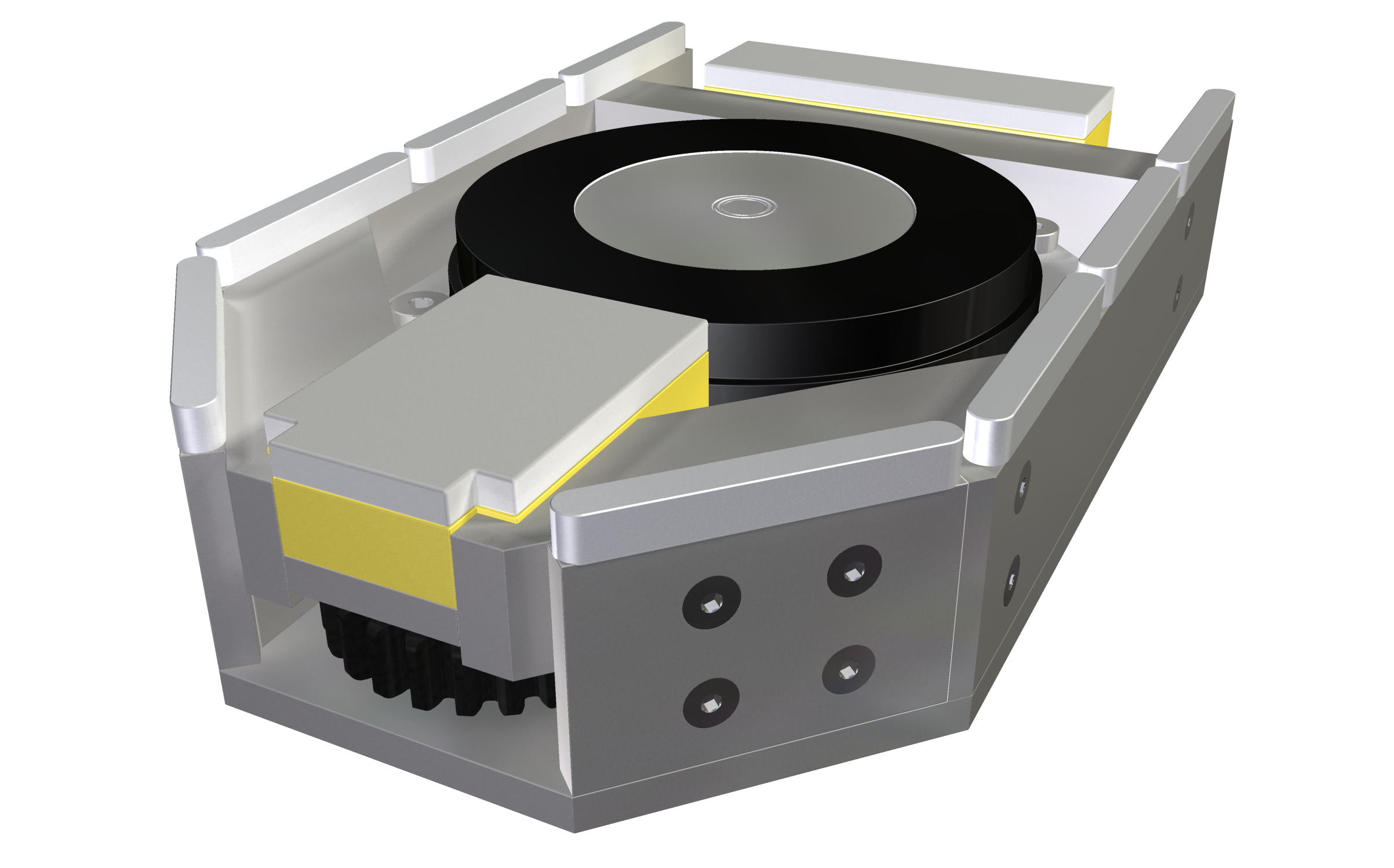
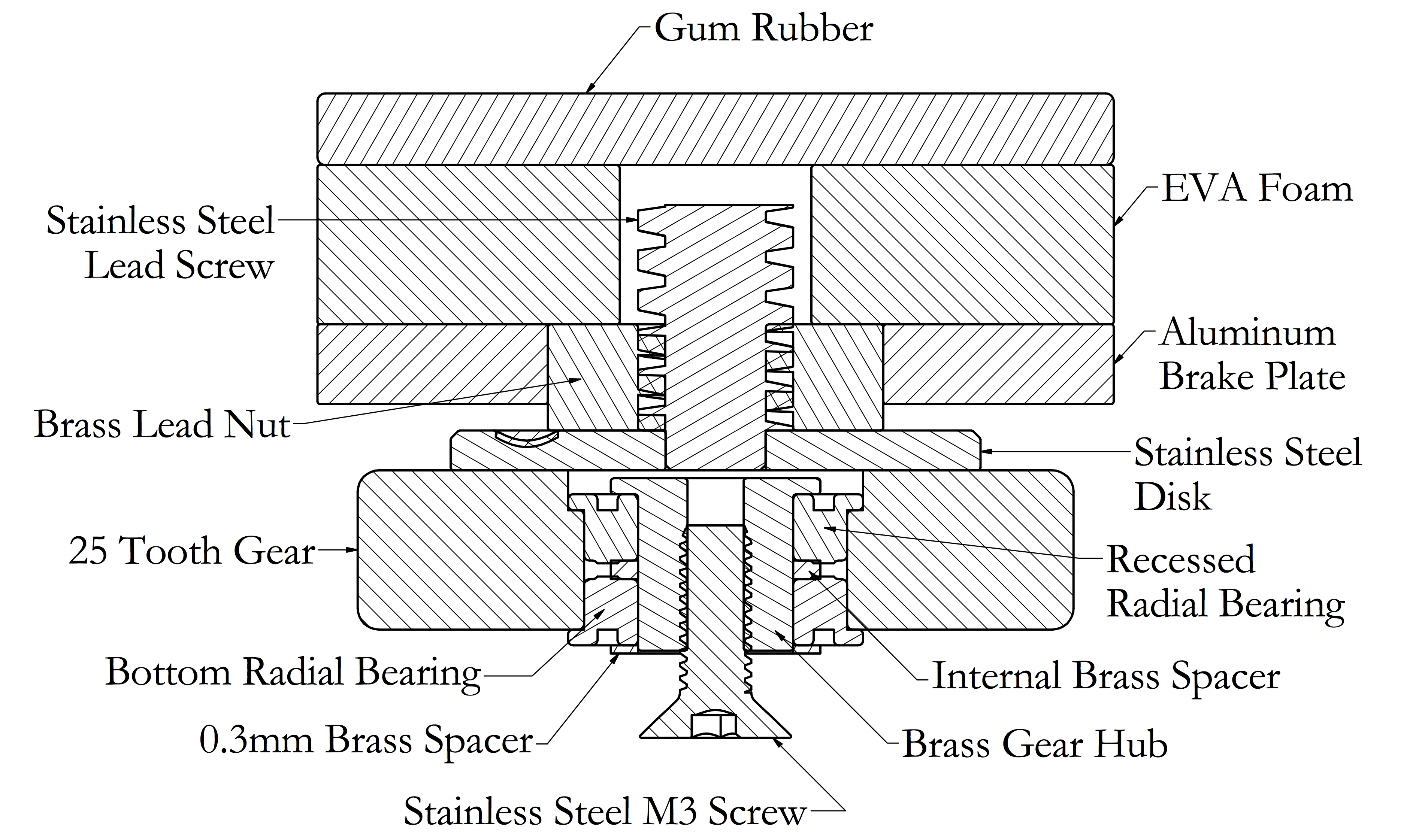
The device is a mechanism that fits in the sole of a shoe and dynamically simulates the friction of a full range of surfaces. The creation of this device is motivated by the need for high-fidelity simulation environments for slip scenarios. These are needed to improve balance for conditioning and rehabilitation reasons, with such a large number of the over-65 population suffering fall-related injuries. Additionally, this device could be used in an augmented reality setting, for research and entertainment purposes.
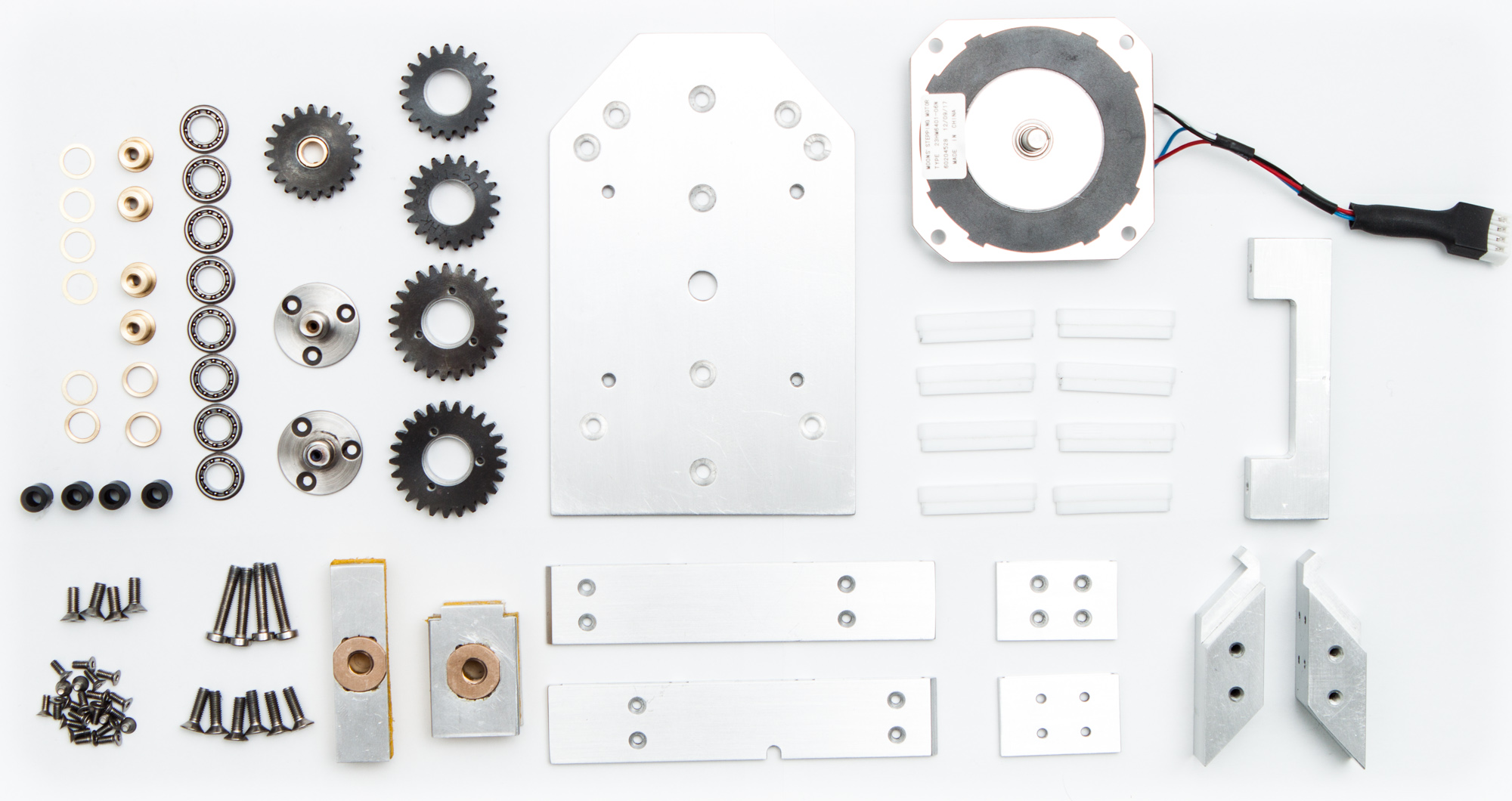
The Device
I simulated a range of surfaces—from ice to concrete—by varying the device’s coefficient of friction using the combination of adjustable, deformable, high-friction brake pads and rigid, static, low-friction Teflon rails. The height of the deformable brakes is adjusted to control the weight distribution between them and the Teflon rails during walking. And because friction force is proportional to normal force—on both the brakes and rails—the device’s net coefficient of friction changes with the brakes’ height.
A central stepper motor drives the gears and a lead screw threaded into each brake changes the height of the braking surface. I developed the drive system myself, and every component except the gears and bearings were machined in-house from aluminum, stainless, and brass. I assembled and tested the mechanism at McGill’s Centre for Intelligent Machines, and our publication is in the works pending the results of further tests. Additionally, the mechanism is being processed for a patent.